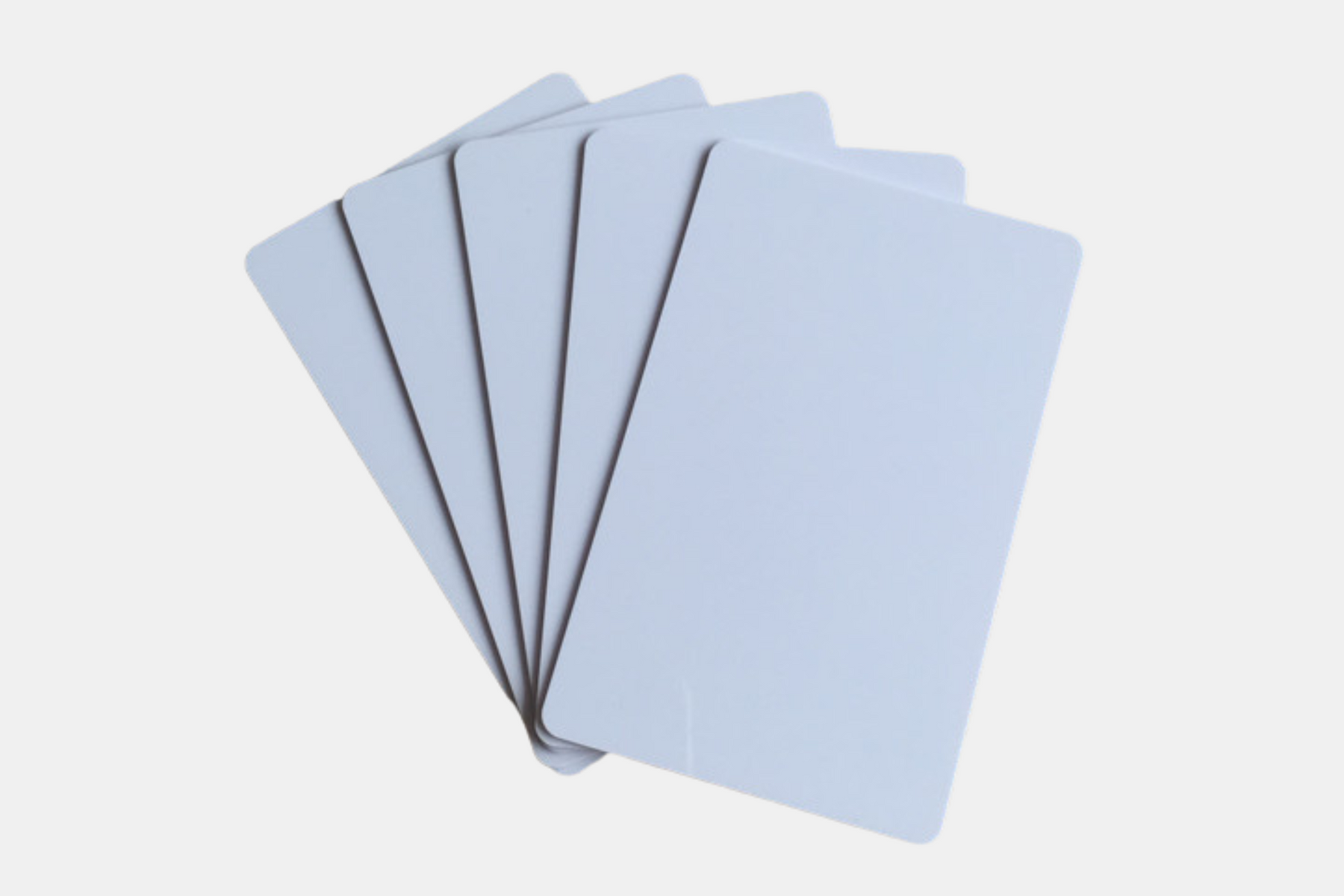
How are plastic cards made?
In today's modern world, plastic cards have become an integral part of our daily lives. Whether it's membership cards, identification cards, access cards, or loyalty cards, we use them for various purposes. However, have you ever wondered how these essential pieces of plastic are manufactured on a large scale?
In this blog, we'll take you on a virtual tour of Card Monster, a leading producer of plastic cards in South Africa. Card Monster produces thousands of cards every year. Let's delve into the intricate process of card production and discover how these small yet significant plastic items are brought to life.
Who is Card Monster, and how do they produce cards?

Card Monster has its headquarters in Johannesburg. The company houses a dedicated team of professionals passionate about innovation and customer satisfaction. Over the years, Card Monster has diversified its product offerings to cater to various industries, including finance, retail, healthcare, hospitality, and transportation.
Card Monster produces cards by having factories in South Africa that make the best quality cards at affordable rates. We manufacture locally and ensure that our products satisfy our customers.
Let's dive into the production process and explore how Card Monster achieves excellence in crafting high-quality plastic cards.
The Initial Stages: From Concept to Design

The journey of plastic card production begins with creating a unique design. Clients collaborate with Card Monster's skilled design team to visualise and create artwork that perfectly represents their brand identity.
During this stage, colours, logos, fonts, and security features are carefully incorporated into the design to reflect the card's intended use.
Read our blog: “Tips on designing eye-catching loyalty cards for your customers”, to see how to design cards that will make your customers buy from you.
Card Monster takes utmost care to ensure that the design meets printing specifications, guaranteeing a flawless end product. Client feedback and intricate design processes help refine the artwork until it perfectly matches the client's vision.
Clients will either have their design ready or they will ask one of our specialised team members to bring their vision to life through collaboration.
We then produce your cards for you.
How are Plastic Cards made?
Below is a breakdown of the manufacturing process of a plastic card:
- The plastic core and laminate materials are mixed and cast into sheet form.
- The core is printed with the appropriate information from the client's design.
- The laminates are applied to the core with heat and pressure.
- The assembled sheet is cut into individual cards.
- The cards are sent to the client.
What is the composition of a plastic card?

The composition of a plastic card typically involves multiple layers of materials carefully laminated together to create a durable product. The most common type of plastic used in card manufacturing is polyvinyl chloride (PVC), but variations may include other materials to enhance specific features or add security elements.
Overlay or Lamination Layers
The overlay layer is found on top of the card. It is made of clear PVC. The overlay layer is transparent. It is applied to protect the printed artwork and the card's core from physical damage and fading over time. This layer ensures the card's longevity and resistance to wear and tear.
Core Layer
Polyvinyl Chloride (PVC) is the primary material used for the core layer of plastic cards. The core contains a resin called polyvinyl chloride acetate (PVCA) that is mixed with materials, dyes and plasticisers. This core material is laminated with thin PVCA or clear plastic layers. These laminates will bind to the core when applied with pressure and heat.
Binding provides flexibility, durability, and a smooth surface for printing. The PVC core has text and graphics printed on it.
Printing Layers
Printing Inks: Various printing inks, including cyan, magenta, yellow, and black (CMYK), are used to create the card's design and artwork. High-quality printing is essential to achieve vibrant colours and sharp images on the card's surface.
Optional Security Features

Cards need security feature layers to protect them from counterfeiting, tampering, and unauthorised access. These security features add an extra layer of protection, making it more difficult for fraudsters to duplicate or alter the cards for illegal purposes.
Here are a few security features we include on our cards:
- Holographic foils - hot stamped technology.
- Watermarks - unique logo or text that can only be seen when moved into the light.
- UV inks - visible only under a UV lamp.
- Micro text - pre-printed text can only be read with magnification or with UV exposure.
- Tactile Impression - die to stamp an impression on the card. Die will be of logo or picture placed onto a card.
- Lamination - once the card is printed, an overlay layer can be applied. The lamination can be unique so that it cannot be copied.
Optional Embossing
Raised Characters: In certain cards, like credit or account cards, embossed characters (raised lettering or numbers) may be added to the surface. Embossing provides a tactile element and helps cardholders identify essential information by touch.
Optional Magnetic Stripe or Chip Layer
Magnetic Stripe: Some plastic cards, such as credit and access cards, may have a magnetic stripe on the back. The stripe contains encoded data, allowing the card to interact with magnetic card readers.
Chip: Alternatively, some cards may incorporate an embedded chip (smart chip) on the surface. This chip stores encrypted data and enables more secure and advanced interactions with card readers.
Optional Signature Panel
Signature Panel: Certain cards, like membership or loyalty cards, may feature a designated space for the cardholder's signature. This panel allows the cardholder to provide a handwritten signature as an additional authentication measure.
Optional Barcodes or QR Codes
Barcodes or QR Codes: Some cards may include barcodes or Quick Response (QR) codes with specific information.
These codes can be scanned for various purposes, such as membership verification or product tracking.
It's important to note that the composition of plastic cards may vary depending on the specific card's intended use and the desired security features. Advanced card technologies and manufacturing processes continually evolve, creating more sophisticated and secure plastic cards. The composition outlined above serves as a general framework for understanding the fundamental components of plastic card production.
Encoding and Personalisation

Personalisation is a crucial aspect of plastic card production, as each card needs to be unique to its holder.
Card Monster employs data encoding techniques to embed personalised information, such as names, account numbers, and expiration dates, onto the card's magnetic stripe or embedded chip.
This data encoding is carried out strictly following data protection regulations, ensuring the security of sensitive information.
Overall, encryption is a vital tool in securing plastic cards and the sensitive information they carry. By encrypting data during transmission and storage, plastic cards are better protected against various forms of cyberattacks, ensuring a safer and more secure payment experience for cardholders.
Quality Control and Inspection

Cards undergo rigorous quality control checks before cards leave the production facility. Card Monster has a robust quality assurance process that includes thorough inspections and sample testing. This step ensures that every card meets the highest standards of quality and accuracy before reaching the client.
Packaging and Delivery
Once the cards pass stringent quality checks, they are carefully packaged to protect them during transit.
Card Monster utilises eco-friendly and secure packaging materials to ensure the cards reach their destination in pristine condition.
The delivery process is efficient, with Card Monster committed to meeting the client's timelines and ensuring prompt and reliable distribution.
Conclusion

Plastic card production is a complex and fascinating process, combining technology, craftsmanship, and innovation. Card Monster's commitment to excellence has made it a leading producer of plastic cards in South Africa, supplying cards to various industries.
From the initial design stage to the final quality control checks, each step in the production process plays a critical role in crafting durable, secure, and visually appealing plastic cards. Card Monster's dedication to customer satisfaction and cutting-edge technology ensures that its cards are a testament to precision and quality, making them essential tools in our modern world.
Please contact us for more information on the cards you want to create with us.
References
- Chen, J. 2023. “Credit Card Encryption: What It Is and How It Works”. https://www.investopedia.com/terms/c/credit-card-encryption.asp.
- Johnstone, S. 2023. “Tips for Designing Eye-Catching Loyalty Cards for Your Customers”.https://www.cardmonster.co.za/blogs/news/tips-for-designing-eye-catching-loyalty-cards-for-your-customers.
- Kagan, J. 2020. “Embossed Card Definition, How It Works, History.” https://www.investopedia.com/terms/e/embossed-card.asp#:~:text=As%20noted%20above%2C%20embossed%20cards,generally%20credit%20and%20debit%20cards.
- Evolis. 2014. “Card lamination”.
- Entrust. 2023. “The Tactile Impression Module Overview”.
- ID card centre. 2023. “Micro Text or Nano Text”.
- Swype. 2021. “New feature to our extensive plastic card portfolio: UV Ink- for enhanced security”
- Digital ID. 2015. “Adding a Watermark to Your Plastic Cards”.
- Nova Vision. 2023. “Holographic Foil”.
Leave a comment